Creating a lower carbon future in the Lower Aire Valley
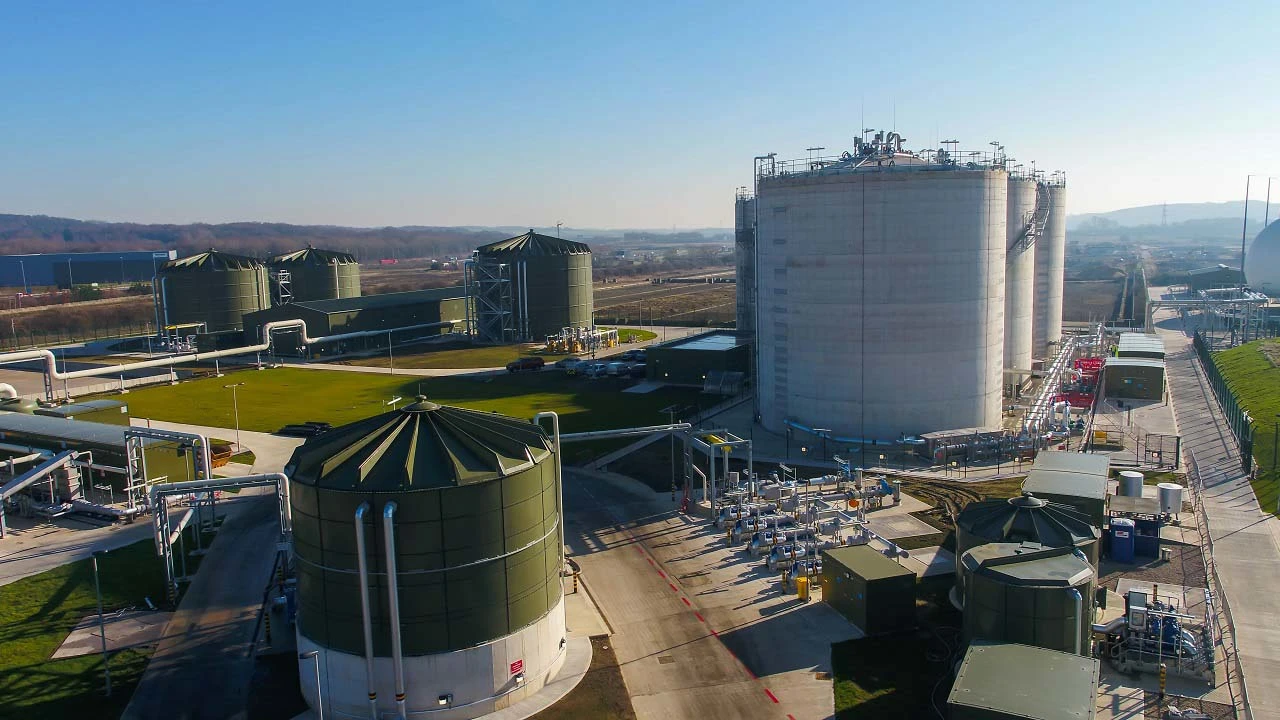
- Project Name
- Knostrop Energy & Recycling Facility
- Location
- Yorkshire, United Kingdom
- Client
- Yorkshire Water
Using carbon-neutral biogas to power treatment process helps UK utility hit sustainability goals
Yorkshire Water’s £72 million Knostrop Energy & Recycling Facility turns wastewater into energy, generating sufficient electricity to power 7,600 homes. The project, according to local member of parliament Hilary Benn, “is helping to create a lower carbon future in the Lower Aire Valley."
The project to create the facility, which saves the client £1.6 million a year in operating costs by meeting 55 percent of the site’s energy needs, was delivered on time and to budget.
This level of execution certainty demonstrates clearly the benefits of using a delivery partner with the ability to add value at multiple points during the asset’s lifecycle.
ㅤ
Early engagement reaps benefits
Black & Veatch’s involvement began early, with a feasibility study to review sludge treatment technologies and identify the best location for the new facility. Mesophilic anaerobic digestion, a proven digestion technology able to generate renewable energy using carbon-neutral biogas, was deemed most suitable.
With technology and location agreed, Black & Veatch helped progress the project by developing an outline design, and undertaking site investigations. The latter work allowed the team to identify and mitigate risks early in the project. For example disused mine workings and contaminated ground were avoided by revising the site layout.
Other preliminary support included an Environmental Impact Assessment to assist the utility’s planning department, in consultation with Leeds City Council planners, in understanding the project’s visual impact.
ㅤ
Designed with efficient operation in mind
Following a mini competition, and negotiated tender, Yorkshire Water awarded Black & Veatch the contract to design and build the Knostrop Energy & Recycling Facility. With client and delivery partner having already collaborated on earlier phases of the project’s lifecycle relationships and trust had been established, and there was already a clear understanding of the utility’s goals for the project, extending beyond construction and into the asset’s operation and maintenance.
QR coded tags were attached to equipment allowing maintenance teams to scan the tag and download asset data to hand-held devices displaying maintenance details. This planned maintenance regime greatly improves the asset’s resilience.
ㅤ
Ensuring efficiencies in construction
Black & Veatch was also able to add value during the construction and procurement phase. The company negotiated a number of single-source subcontracts for civil engineering, tanks and electrical suppliers during the tender. Collaborative working with these key supply chain partners allowed procurement time and cost on the project to be reduced. Several subcontracts were placed with local companies providing economic and social value to the area.
Offsite manufacture was used for chemical dosing equipment, access metalwork and the combined heat and power units. This improved construction productivity, quality and allowed for manufacture in a controlled environment. The boiler house was subcontracted as one package for all the MEICA equipment eliminating the need to manage construction interfaces.
The scope for the tank packages included the construction of the bases eliminating an interface, which along with specialist formwork allowed successive productivity improvements on the four digesters.
The project’s embedded carbon footprint was reduced by recycling 120,000 cubic metres of filter media as bedding material rather than being disposed of in landfill.
According to Mark Baker, Head of Asset Solutions for Yorkshire Water, “Black & Veatch have worked collaboratively with our Asset Management business unit to deliver a flag ship project. Knostrop significantly contributes towards our Performance Commitment for energy generation and carbon reduction.”
Contact Us
Looking for a partner in innovation?
Let's Talk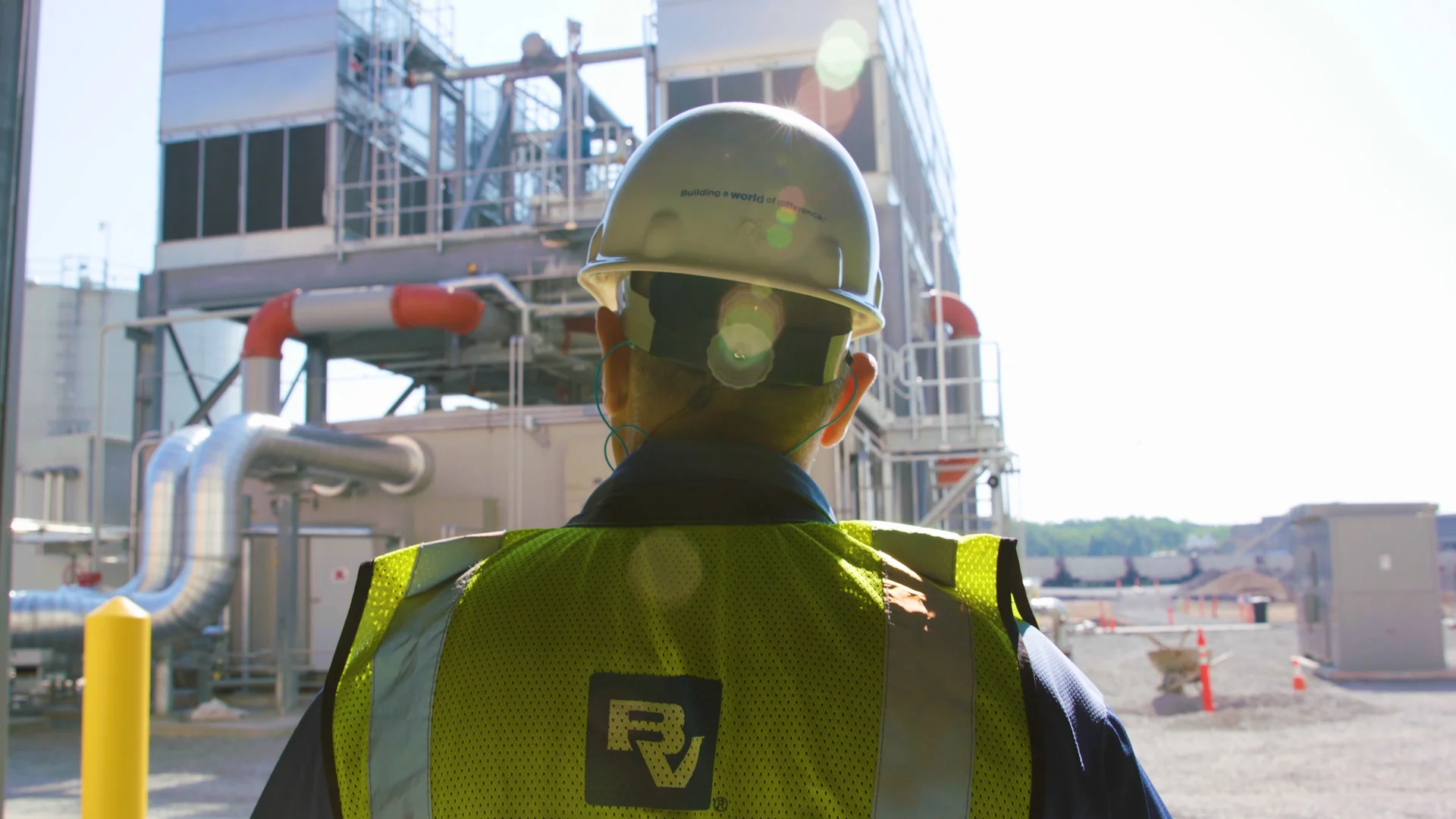